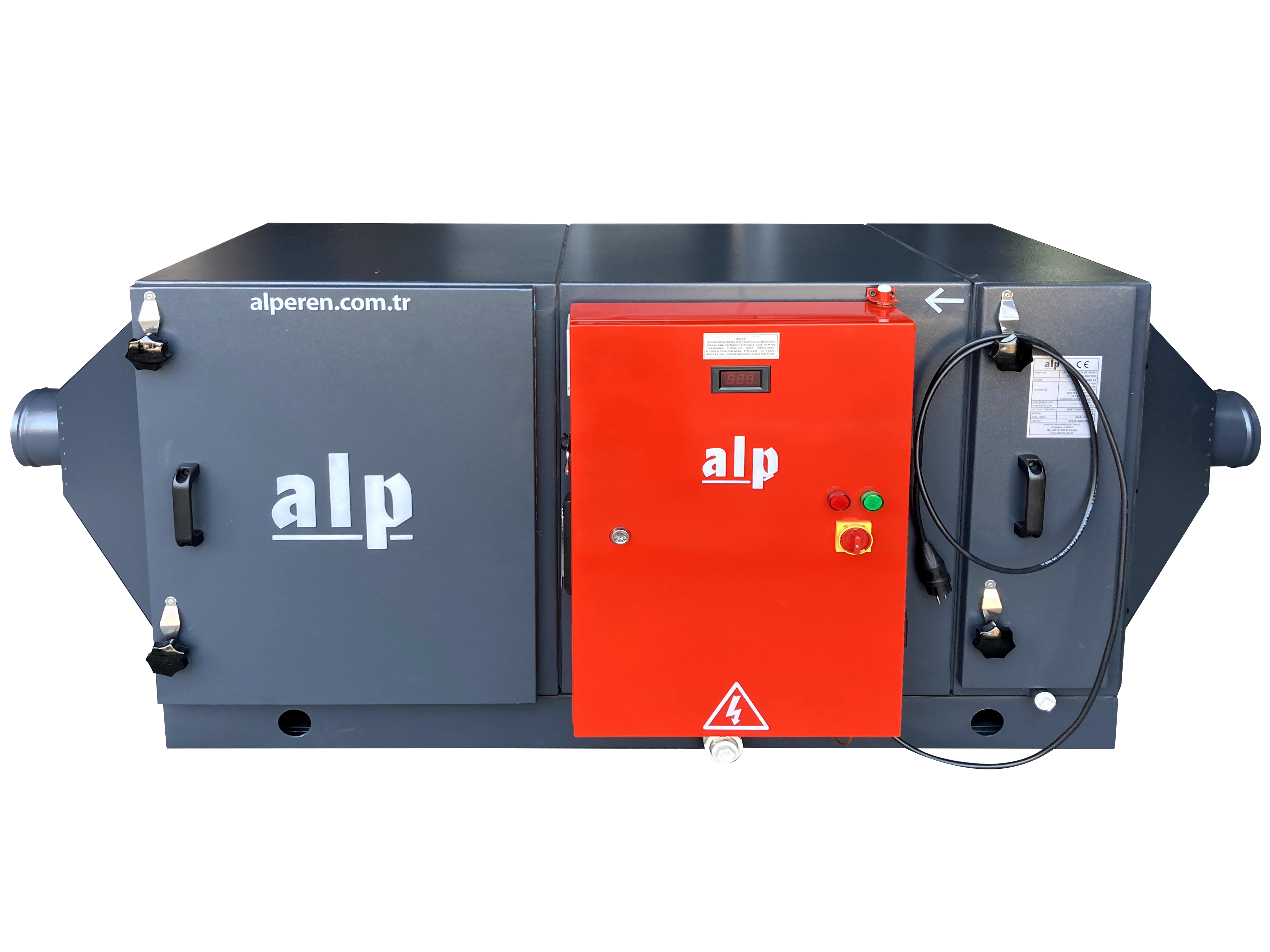
Filter Selection in Laser Cutting Units
Laser cutting technology is widely used in industrial manufacturing processes that demand high precision and efficiency. However, these systems generate various airborne contaminants, including fumes, gases, fine particles, and odors, which can adversely affect both equipment performance and operator health. Implementing effective air filtration systems is crucial to mitigate these risks.
Importance of Filtration in Laser Cutting Units
During laser cutting operations, materials such as metals, plastics, and composites are vaporized, releasing hazardous substances into the air. These emissions can lead to respiratory issues for operators and accumulate on machine components, reducing their lifespan. Proper filtration ensures a safer working environment, maintains air quality, and prolongs equipment durability.
Common Filter Types Used in Laser Cutting Units
-
HEPA Filters (High-Efficiency Particulate Air Filters)
HEPA filters are designed to capture at least 99.97% of airborne particles as small as 0.3 microns. They are highly effective in removing fine dust and particulate matter generated during laser cutting processes.
Applications:
-
Metal processing facilities, especially those involving laser cutting operations.
Advantages:
-
High efficiency in trapping fine particles.Reddit+1RoboVent+1
-
Enhances air quality and protects sensitive equipment components.Activated Carbon Depot
Considerations:
-
Requires periodic replacement as filters become saturated.Reddit+2hpclaser.co.uk+2Wikipedia+2
-
-
Activated Carbon Filters
Activated carbon filters are effective in adsorbing volatile organic compounds (VOCs), odors, and gaseous pollutants emitted during laser cutting, particularly when processing plastics and other synthetic materials.
Applications:
-
Environments where laser cutting of plastics, acrylics, or other materials that release odors and gases is performed.sawmillcreek.org
Advantages:
-
Efficient in removing odors and harmful gases.
-
Improves overall air quality in the workspace.
Considerations:
-
Filter lifespan varies based on usage and concentration of pollutants; regular monitoring and replacement are necessary.
-
-
Electrostatic Filters
Electrostatic filters utilize electrostatic charges to attract and capture particles from the air. They are particularly useful for trapping fine dust and smoke particles generated during laser cutting.
Applications:
-
Facilities with significant dust and smoke production from laser operations.
Advantages:
-
Reusable after cleaning, offering cost savings over time.
-
Effective in capturing fine particulate matter.
Considerations:
-
Regular maintenance and cleaning are required to maintain efficiency.
-
-
Bag and Roll Filters
Bag and roll filters are designed to capture larger particles and serve as pre-filters in multi-stage filtration systems. They help extend the life of more sensitive filters like HEPA and activated carbon filters.
Applications:
-
Industrial settings with high volumes of coarse dust and debris.
Advantages:
-
Cost-effective solution for large particle filtration.ulsinc.com+2airpurifiersandcleaners.com+2fumeextractor.en.made-in-china.com+2
-
Easy to replace and maintain.Alperen Mühendislik
Considerations:
-
Not suitable as standalone filters for fine particles or gases; typically used in conjunction with other filters.
-
Factors to Consider When Selecting Filters
-
Type of Contaminants
Identify the specific pollutants generated by your laser cutting processes, such as particulate matter, VOCs, or odors, to choose appropriate filters.
-
Filtration Efficiency
Consider the efficiency ratings of filters, such as MERV (Minimum Efficiency Reporting Value) or HEPA classifications, to ensure adequate removal of contaminants.
-
Airflow Requirements
Ensure that the selected filters can handle the airflow rates of your laser cutting equipment without causing excessive pressure drops.
-
Maintenance and Replacement
Evaluate the maintenance needs and replacement frequency of filters to plan for operational downtime and costs.
-
Compliance with Regulations
Ensure that your filtration system meets local and industry-specific environmental and safety regulations.
Conclusion
Selecting the appropriate filtration system for laser cutting units is essential for maintaining air quality, ensuring operator safety, and prolonging equipment life. A combination of filters, such as pre-filters, HEPA filters, activated carbon filters, and electrostatic filters, may be necessary to effectively address the range of contaminants produced during laser cutting operations. Regular maintenance and monitoring of these systems will ensure continued efficiency and compliance with health and safety standards.
Ilker KURAN
Alperen Engineering Ltd.