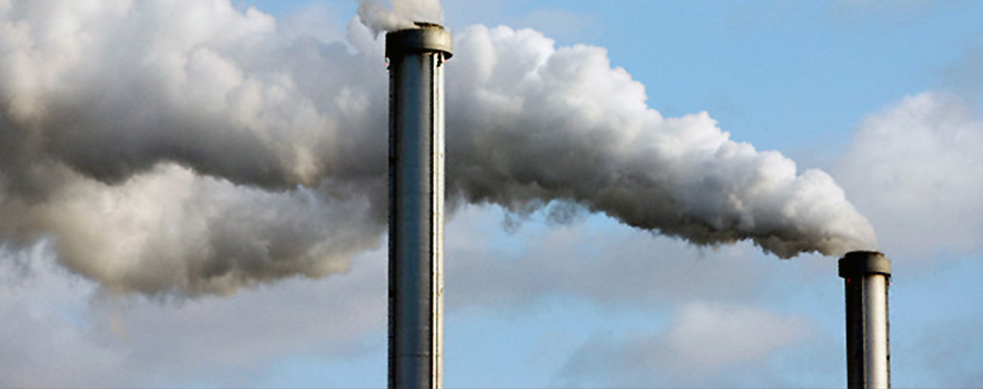
The oil fumes and unwanted odors that occur during the production process pose serious risks to the health of employees and the environment, as well as affecting the quality of machines and products.
During the thermofixing and drying processes applied in the fabric dyehouses of textile factories, oil particles that pollute the environment and the gases that are harmful to human health are discharged from the chimneys of the stenter machines into the atmosphere.
When working on viscose and cotton fabrics in fabric production facilities, pre-washing and desizing processes are carried out. Pre-washing is a part of the dyeing process and is a prerequisite for a healthy dyeing. The fabric balls that are pre-washed are passed through the raw cloth opening machine to be sent to the dyeing machines. Cloth balls are added to each other and transferred to dyeing machines. Fabrics are dyed in dyeing machines in two ways: disperse and reactive dyeing. While reactive dyeing is used only for dyeing cellulosic fabrics, disperse dyeing is used for non-cellulosic fabrics.
Desizing process is applied on polyester fabrics to be dyed in the facility. After dyeing the fabric, rinsing is performed and the fabric is laid on the rope opening machine.
For the purpose of drying, the fabric is transported to the Ramöz machine in a transverse direction, attached to its edges. Pressurized and humid hot air is sprayed on both surfaces of the stretched fabric and the fabric is dried with the help of a special vacuum device. Afterwards, the dried fabric is taken to the printing process and the fabrics that are removed from the printing are checked in quality control machines, packaged and made ready for shipment.
The section where intense smoke, high temperature, humidity and odor occur in the ram machines is the section where the fixing and drying processes are located.
Pollutant factors such as CO carbon monoxide, NOX nitrogen oxides, SO2 sulfur dioxide, VOC, dust and volatile organic compounds in the exhaust air after the drying phase in the ram machines create air emission that must be filtered. The main pollutant of odor emission is volatile organic compounds, also known as VOCs.
In other words, in stenter machines, pressurized hot air is sprayed on both surfaces of the fabric and the fabric is dried with the help of a special vacuum device. Brightening, dyeing, grinding etc. applied to fabrics. The polluted air and high temperatures that are released during the processes pose risks for businesses. The fabric is treated at high temperatures during pretreatment. These high temperatures, which are obtained at high costs, are discharged to the outside while exhausting the unwanted odor and smoke. This situation creates high financial losses for the business.
The temperature obtained from the waste gases generated in the stenter chimney can be put into use in four different ways, optionally.
Hot water obtained by the heat exchanger, which has the principle of air / water operation, in the paint shop or any area where hot water is needed, or,
In the pre-heating of the air by returning the hot air obtained by the heat exchanger, which has the principle of water / air operation, to the Ram machine, or,
In the pre-heating of the air by returning the hot air obtained by the heat exchanger, which has an air / air working principle, to the Ram machine, or,
The hot water obtained with the heat exchanger, which has the principle of air / water operation, can be used in any area where hot water is needed by using the plate heat exchanger or in the preheating of the air by returning it to the Ram machine.
When an ideal filter system is used in stenter chimneys;
A clean production plan is provided by filtering the emissions into air, water and soil as a result of industrial activities carried out by using natural resources, raw materials, water and energy.
Energy use is significantly reduced and there is a significant reduction in waste generated.
High environmental benefit is provided in terms of smoke and odor emissions.
VOCs etc. in the stenter exhaust air. By reducing the values of organic compounds, odor emissions are reduced up to 99%.
Thanks to the heat recovery unit, up to 15% of natural gas consumption is saved.
Compared to other filtration techniques 42-52% in water consumption, 11-25% in energy consumption, 15-38% in chemical substance consumption, 40-53% in waste water generation, 24-46% in chemical oxygen demand load, 17% in waste flue gas emissions. 48 and 9-21% reduction in solid waste generation is predicted.
It is predicted that the amortization period of an ideal filter system will decrease between 12-24 months compared to other filtration systems.
Waste oils formed during the fixing of fabrics are considered as industrial waste oil.
A high level of eco efficiency is created.
Stenter chimney filtration systems should be designed considering the pollutants such as heavy oil smoke, odor, high temperature and VOC that occur in polyester and polyester elastane fabrics.
It is also recommended by the Provincial Local Environmental Boards to install electrostatic filters and deodorizing filters in the chimneys of these machines in order to prevent smoke and odor emissions from Ram machines operating in the textile sector and especially pre-fixing or fixing using polyester fabric.
In addition to protecting the environment and human health by using advanced technology filter systems such as pre-filter units, intermediate filter units, electrostatic filter units, plasma ionizer filter units, ozone filter units in order to filter the dense smoke, oil and odor formed in the chimneys of the ram machines at the maximum level. It is possible to recover the textile oils used in warp, transfer, cone, texturing, giping processes that are thrown out with the flue gases and to provide high energy savings.
İlker KURAN
Alperen Ltd. Şti.